Struggling with storage in warehouse environments is a common hurdle many businesses face. The challenge of effectively organizing and managing inventory in these spaces can seem endless. But there's a light at the end of the tunnel: strategic and innovative solutions are here to turn these storage obstacles into opportunities for operational excellence.
RCS Moving & Storage stands at the forefront of reimagining storage in warehouse settings. We're not just about stacking boxes; we're about transforming your warehouse into a hub of efficiency and productivity. Our expertise in warehouse storage solutions is tailored to meet your unique business needs.
Embark on a journey through this article to explore the realms of efficient storage in warehouse environments. We'll guide you through a suite of strategies from optimizing space to leveraging the latest technology, all designed to enhance your warehouse's functionality. Let's navigate the world of warehouse storage together and unlock the full potential of your space.
Assessing Warehouse Storage Needs
The first step to warehouse efficiency is a thorough assessment of storage needs. This not only involves a deep dive into current inventory types and volumes but also a forward-looking approach to anticipate future demands. This dual focus ensures a robust and adaptable storage system that can evolve with your business.
Understanding the Importance of Inventory Analysis
Inventory analysis is a process involves a deep understanding of the types of inventory you have and their respective volumes. By conducting a thorough inventory analysis, you can pinpoint the most suitable storage solutions, ensuring that every item is stored efficiently and accessibly. This analysis is crucial in crafting a storage strategy that is not only tailored to your current inventory but also adaptable to future changes.
- Cataloging Inventory Types: Start by categorizing your inventory. This could include raw materials, finished goods, perishable items, or high-value products. Understanding the different types of inventory you have is crucial in determining the appropriate storage methods. For instance, perishable goods may require refrigerated storage, while high-value items might need secure, locked storage.
- Volume and Size Assessment: Measure the volume and physical dimensions of your inventory. This step helps in determining how much space each type of inventory will occupy. For example, bulky items might be best suited for pallet racking systems, while smaller items could be stored more efficiently on shelving units.
- Frequency of Access: Analyze how often each inventory type is accessed. Fast-moving items should be stored differently from slow-moving ones. Items that are accessed frequently should be stored in easily accessible locations to speed up the retrieval process and improve overall efficiency. Conversely, items that are rarely accessed can be stored in less accessible areas, optimizing the use of space.
- Seasonal Variations: Consider any seasonal variations in your inventory levels. Many businesses experience fluctuations in stock levels due to seasonal demand, promotional events, or market trends. By accounting for these variations, you can ensure that your storage system can adapt to changing inventory levels without compromising efficiency.
- Future Inventory Projections: Incorporate future inventory projections into your analysis. Understanding how your inventory levels and types might change in the future is vital for creating a scalable and flexible storage solution. This foresight prevents the need for frequent overhauls of your storage system, saving time and resources in the long run.
The Crucial Role of Future Demand Planning
Future demand planning in warehouse management is key to aligning storage solutions with evolving business needs. This strategic foresight ensures warehouses are equipped to handle future growth and market shifts, maintaining efficiency and customer satisfaction. By anticipating changes in storage needs, warehouses stay ahead of potential space and logistical challenges.
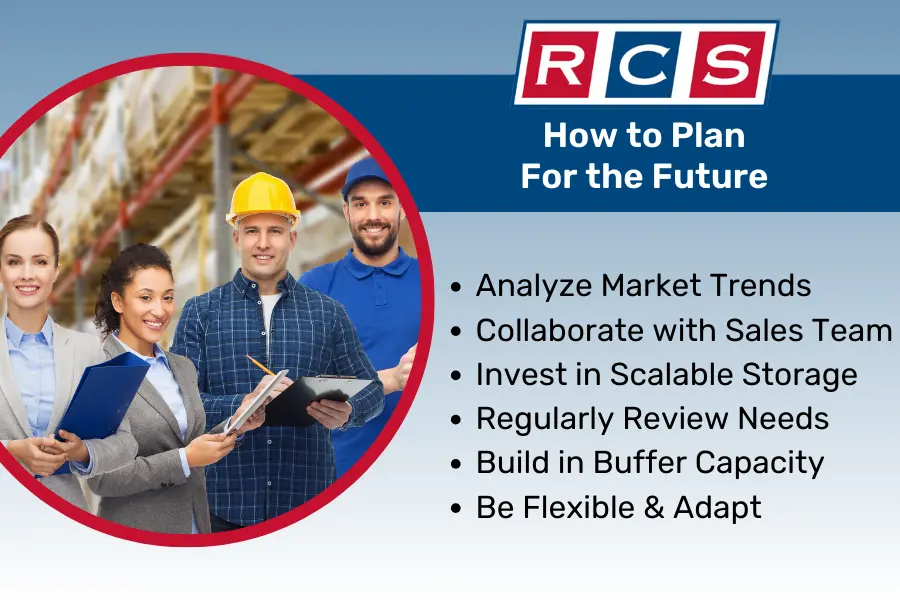
- Analyzing Market Trends and Forecasting Demand: Use historical sales data, market research, and predictive analytics to understand potential increases or decreases in product demand. This analysis helps in anticipating changes in inventory levels and types, allowing you to adjust your storage solutions accordingly.
- Collaborating with Sales and Marketing Teams: Collaborate with your sales and marketing teams to gain insights into upcoming promotions, new product launches, or seasonal fluctuations. These departments can provide valuable information about expected changes in inventory levels, enabling you to prepare your warehouse for increased or specialized storage needs.
- Investing in Scalable Storage Solutions: Opt for storage solutions that can be easily scaled up or down. Modular shelving, adjustable racking systems, and mobile storage units are examples of flexible solutions that can accommodate changing inventory levels without the need for extensive overhauls.
- Regularly Reviewing and Adjusting Plans: Make future demand planning an ongoing process. Regularly review and adjust your storage plans to align with the latest business forecasts and market conditions. This dynamic approach ensures that your warehouse is always prepared for future demands.
- Building in Buffer Capacity: Plan for buffer capacity in your warehouse to accommodate unexpected surges in inventory. This might involve reserving extra storage space or having the ability to quickly deploy additional storage solutions when needed.
- Training Staff for Flexibility and Adaptation: Train your warehouse staff to be flexible and adapt to changing storage needs. A well-trained team can quickly and efficiently reorganize storage layouts, handle new types of inventory, and maintain operational efficiency even as demands shift.
A Guide to Selecting the Right Warehouse Storage Systems
Selecting the right storage systems is pivotal in maximizing efficiency and productivity in warehouse operations. From the versatile pallet racking systems to the more specialized push-back racking, understanding and choosing the right storage solutions play a crucial role in optimizing storage in warehouses.
- Pallet Racking: A versatile solution for warehouses with varied inventory types and high turnover. Pallet racking uses vertical space efficiently and provides easy access to stored items, making it ideal for a wide range of products and facilitating quick inventory turnover.
- Shelving vs. Racking: Differentiate between shelving for lighter items and racking for heavier loads. This distinction is key to optimizing storage in warehouse environments and ensuring the right system is used for the right inventory, thereby enhancing organization and safety.
- Push-Back Racking: Ideal for high-density storage, push-back racking allows deeper storage and efficient space utilization, making it a valuable asset for warehouses with limited space. It enables storing multiple pallets deep, increasing storage density while allowing for easy access.
- Drive-In and Pallet Flow Racking: These systems are designed for high-density storage. Drive-in racking is perfect for storing large quantities of similar products, reducing aisle space and increasing storage capacity. Pallet flow systems, on the other hand, use gravity rollers for automatic stock rotation, ideal for perishable goods.
Revolutionizing Warehouse Operations with Technology
Integrating advanced technological solutions transforms storage in warehouse settings, elevating efficiency, accuracy, and adaptability to unprecedented levels. This digital evolution reshapes how warehouses operate, making them smarter, more responsive, and equipped to handle the complexities of modern logistics and supply chain demands.
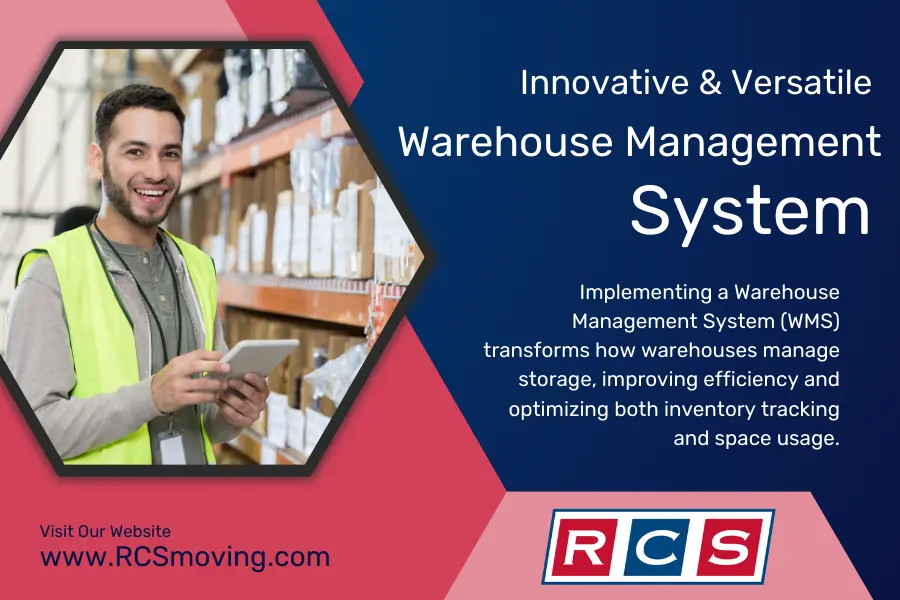
- The implementation of Warehouse Management Systems (WMS): Plays a pivotal role in revolutionizing storage management in warehouses. By providing real-time data on inventory, WMS enhances the efficiency and accuracy of warehouse operations. This system not only optimizes space utilization but also streamlines order processing and inventory management.
- Real-Time Inventory Tracking: WMS offers up-to-date information on inventory levels, location, and movement, enabling precise stock management and reduced risk of overstocking or stockouts. This feature is crucial for maintaining inventory accuracy and ensuring timely replenishment.
- Enhanced Order Processing: Streamlines the order fulfillment process, ensuring faster and more accurate order handling from storage to shipment. This improvement leads to increased customer satisfaction and operational efficiency.
- Space Utilization Optimization: Maximizes the effective use of warehouse space, ensuring optimal placement and organization of inventory for efficient access and storage. Effective space utilization is key to maximizing warehouse capacity and operational productivity.
- Strategic Stock Placement: Aids in decision-making for inventory placement, leading to quicker retrieval times and minimizing congestion in storage areas. This strategic approach enhances the overall flow and efficiency of warehouse operations.
Embracing Automation and Robotics to Revolutionize Warehouse Storage
The integration of automation and robotics is transforming the landscape of warehouse storage, ushering in a new era of efficiency and precision. By minimizing manual intervention, these technologies not only expedite the storage and retrieval process but also reduce errors and enhance storage capacity. This shift towards automation is pivotal in adapting to the evolving demands of modern warehousing.
- Minimized Manual Handling: Automation and robotics significantly reduce the reliance on manual labor, lowering the risk of errors and enhancing overall operational speed and safety in the storage process.
- Efficient Storage and Retrieval: Automated Storage and Retrieval Systems (AS/RS) optimize the storage process, utilizing vertical space more effectively and increasing storage density, leading to a more organized and space-efficient warehouse.
- Adaptability to Inventory Variations: Robotics technology can handle a wide range of inventory sizes and weights, offering flexible and dynamic storage solutions suitable for diverse warehousing needs.
- Enhanced Operational Efficiency: The use of automation and robotics in storage systems leads to faster, more accurate order processing, contributing to a significant boost in overall warehouse productivity and customer satisfaction. The integration of automation in warehouses streamlines operations, leading to increased efficiency and reduced operational costs.
Strategic Space Optimization for Storage in Warehouses
Space optimization is a key driver of operational excellence, transforming how businesses use their existing infrastructure. This strategic approach to using space effectively leads to a harmonious blend of high-density storage and efficient operational workflow, directly impacting productivity and enhancing the bottom line.
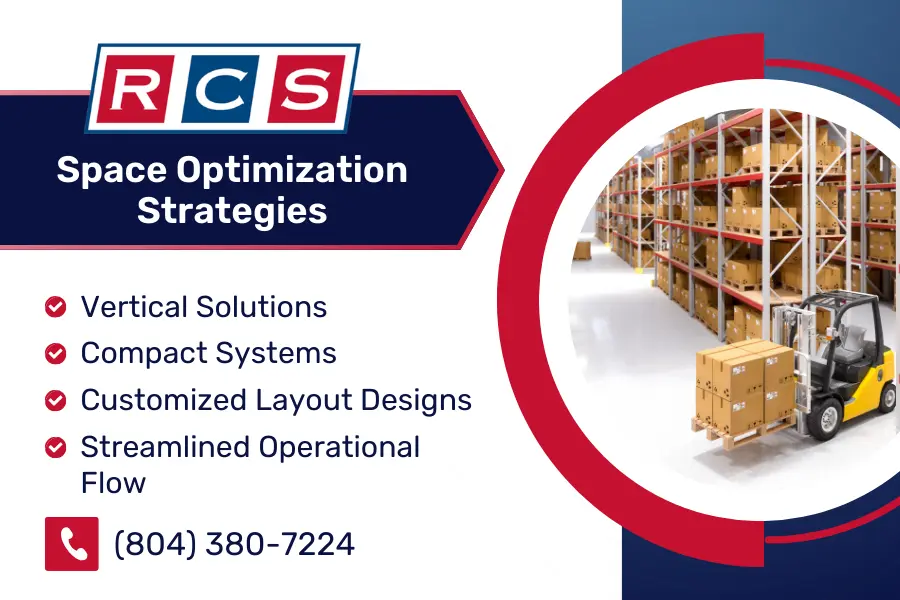
- Vertical Storage Solutions: Implement multi-tiered storage systems to utilize vertical space, greatly expanding storage capacity without needing to increase the warehouse's physical size.
- Compact Storage Systems: Utilize mobile shelving and other compact storage options to maximize space efficiency, especially in smaller warehouse areas.
- Customized Layout Design: Design your warehouse layout specifically to meet your unique storage needs, ensuring optimal use of space and smoother operational processes.
- Streamlined Operational Flow: A well-planned layout not only saves space but also streamlines warehouse operations, leading to faster processing times and enhanced overall efficiency.
Prioritizing Safety in Warehouse Storage
Safety in warehouse storage transcends regulatory compliance; it's a cornerstone of operational excellence. Establishing rigorous safety protocols and conducting consistent safety audits are crucial in creating and maintaining a secure and efficient storage environment. These measures not only protect staff and inventory but also enhance overall productivity.
- Establishing Safety Protocols: Develop and implement comprehensive safety procedures to ensure the well-being of both staff and inventory. A strong focus on safety is essential for maintaining a productive and hazard-free warehouse environment.
- Regular Safety Audits: Conduct systematic safety audits to adhere to safety standards continuously and to identify and mitigate potential risks. These audits play a pivotal role in sustaining a secure and compliant storage atmosphere.
- Continuous Safety Training: Regularly train staff on safety protocols and emergency procedures to foster a culture of safety awareness and readiness within the warehouse. Warehouse safety training courses cover various aspects, including lifting injuries prevention and forklift accident avoidance.
- Investing in Safety Equipment: Equip your warehouse with necessary safety gear and machinery safeguards to prevent accidents and injuries, further reinforcing a safe storage environment. Warehouse safety equipment includes barriers, guards, and protective gear to enhance safety for employees and equipment.
Eco-Friendly Practices in Warehouse Operations
In today's environmentally conscious world, sustainability is a crucial aspect of warehouse operations. Implementing green initiatives not only serves the environment but also boosts the efficiency and reputation of your warehouse. Sustainability in warehousing is becoming a key factor in operational strategy and brand value.
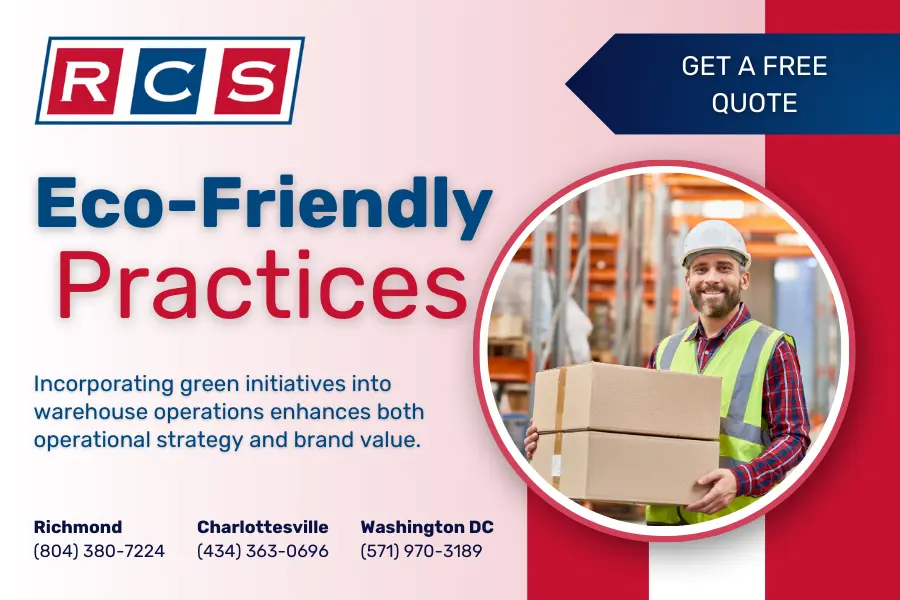
- Recycling and Waste Reduction: Engage in robust recycling programs and minimize waste to demonstrate a commitment to environmental stewardship. These sustainable practices are vital for maintaining an eco-friendly and responsible approach to warehouse storage.
- Energy-Efficient Practices: Implement energy-saving lighting and machinery to lessen the environmental footprint of warehouse activities. These measures not only aid in sustainability but also result in cost savings, adding to the overall efficiency of the warehouse.
- Sustainable Resource Management: Use resources responsibly and opt for eco-friendly materials and processes wherever possible, further promoting sustainable operations.
- Green Building Standards: Where applicable, align warehouse construction and renovation with green building standards, enhancing the sustainability profile of the physical warehouse space.
Choosing RCS Moving and Storage for Your Warehouse Storage Needs
When it comes to optimizing your warehouse storage, choosing RCS Moving and Storage offers a blend of expertise, efficiency, and reliability. Our diverse range of services caters to various storage requirements, ensuring that your inventory is managed with the utmost care and professionalism. Here’s why RCS Moving and Storage that make us the ideal choice for your warehousing needs.
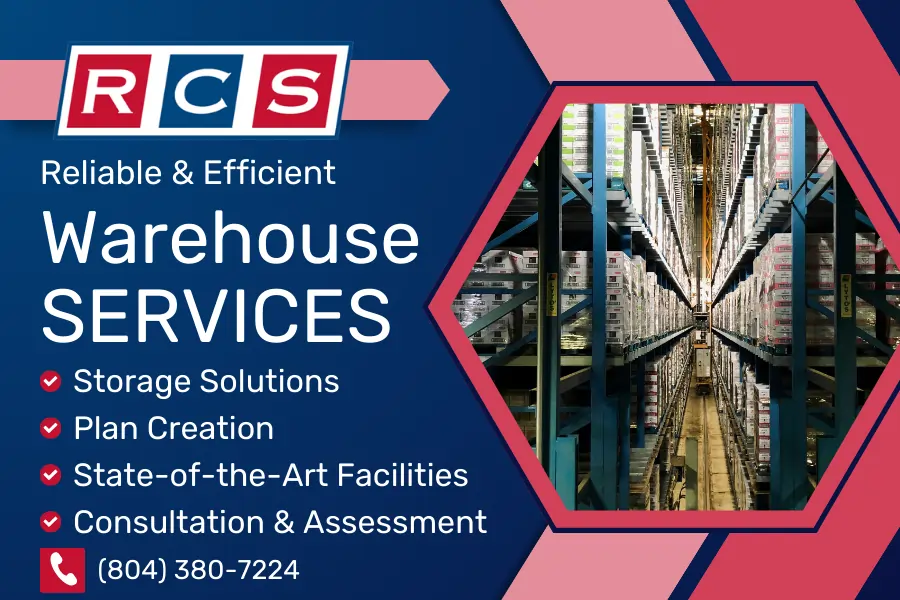
- Comprehensive Inventory Management: We offer detailed inventory analysis, ensuring that each type of inventory is stored according to its specific needs, be it refrigerated storage for perishable goods or secure storage for high-value items.
- Customizable Storage Solutions: Our storage systems are adaptable to your unique requirements, from pallet racking for bulky items to efficient shelving units for smaller goods, ensuring optimal use of your warehouse space.
- Advanced Technology Integration: RCS Moving and Storage utilizes cutting-edge Warehouse Management Systems to provide real-time inventory tracking and streamline order processing, enhancing the efficiency and accuracy of your storage operations.
- Efficient Space Utilization: We specialize in space optimization, utilizing multi-tiered storage systems and compact storage solutions like mobile shelving to maximize your warehouse's storage capacity without expanding its physical footprint.
- Stringent Safety Protocols: Our commitment to safety is evident in our rigorous safety procedures and regular safety audits, ensuring a secure and efficient storage environment for your inventory.
- Sustainability Commitment: At RCS Moving and Storage, we prioritize eco-friendly practices, including recycling programs and energy-efficient systems, to minimize our environmental impact while optimizing warehouse operations.