Facing a warehouse relocation can seem daunting, with the pressures of managing logistics and minimizing downtime weighing heavily on business owners. The challenges of such a move are significant, yet they mark a crucial step towards growth and enhanced efficiency. This guide is crafted to navigate you through these complexities, transforming a daunting task into a smooth, strategic process.
In this landscape of change, RCS Moving and Storage stands as a trusted ally. Their extensive experience in Virginia and North Carolina equips them to tackle the nuances of warehouse relocation, ensuring a seamless transition for your business.
As you read on, you'll gain valuable insights and practical tips to master your warehouse relocation. Each section is designed to equip you with the knowledge and confidence needed for a successful move. Let this guide be your roadmap to a stress-free and efficient relocation with RCS Moving and Storage.
Understanding Your Warehouse Relocation Struggles
Facing a warehouse relocation when the national warehouse vacancy rate has hit an all-time low can feel overwhelming. Despite the tight 3.6% vacancy rate, moving can be a journey of unlocking new potential.
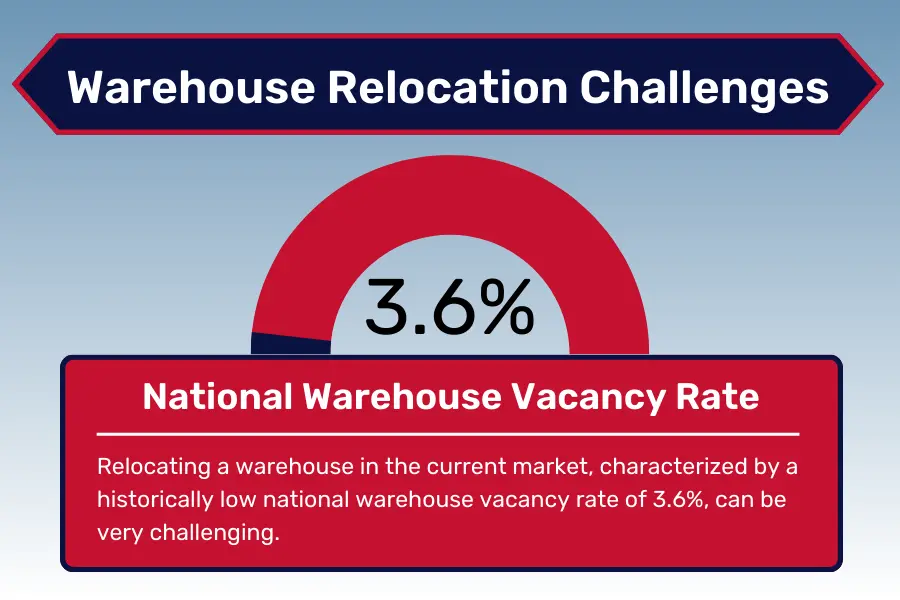
Consider the exciting prospects a new warehouse location brings. Strategically choosing the right location can lead to increased efficiency and innovation. Your move becomes a powerful tool for streamlining operations and expanding your market reach. A new environment can be incredibly uplifting for your team, bringing a sense of renewal and motivation.
Relocating your warehouse, despite the challenges, is an opportunity to reinvigorate your business and pave the way for future success. It's a journey worth embracing, filled with potential for growth and innovation.
Creating a Relatable Warehouse Relocation Plan
Crafting a solid relocation plan is the cornerstone of a successful warehouse move. This process involves strategically transitioning your operations to a new space without missing a beat. A well-thought-out plan ensures your move is smooth and efficient, minimizing disruption to your business.
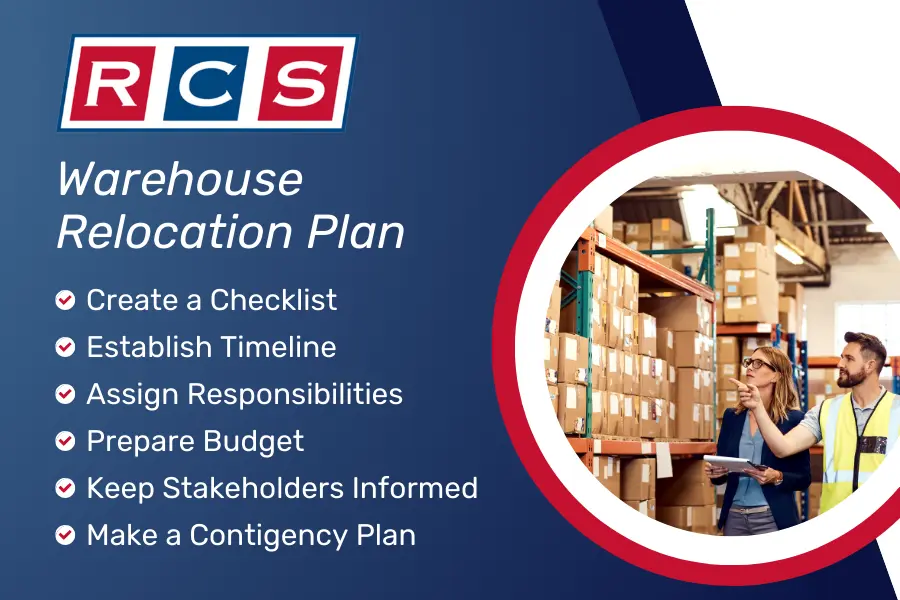
Here are the key steps to a successful warehouse relocation plan:
Develop a Detailed Checklist: Start with creating a comprehensive checklist. This list should include everything from selecting movers to setting the moving date. A detailed checklist is like a roadmap, ensuring you don't overlook any vital steps in the moving process.
Timeline Coordination: Establish a clear timeline for your move. This includes setting realistic deadlines for each stage of the relocation. A well-structured timeline helps keep the move on track and ensures all tasks are completed in an orderly fashion.
Assign Responsibilities: Delegate specific tasks to your team members. This approach helps distribute the workload evenly and keeps everyone involved and accountable. Each team member plays a crucial role in the move, contributing to a collective effort.
Budgeting: Prepare a comprehensive financial plan. This should cover all costs associated with the move, from hiring movers to any equipment upgrades needed in the new location. Effective budgeting is key to managing expenses and avoiding financial surprises.
Stakeholder Communication: Keep everyone informed throughout the process. Regular updates to your team, stakeholders, and clients maintain transparency and build trust. Clear communication ensures that everyone is on the same page.
Contingency Planning: Expect the unexpected and have backup plans ready. Challenges can arise during a move, and having contingency plans in place ensures you can address them swiftly without major disruptions.
Guidelines for Choosing Your Next Warehouse Location
Selecting the ideal warehouse location is a critical decision that impacts both operational effectiveness and customer relations. Here are essential considerations for making a strategic choice:
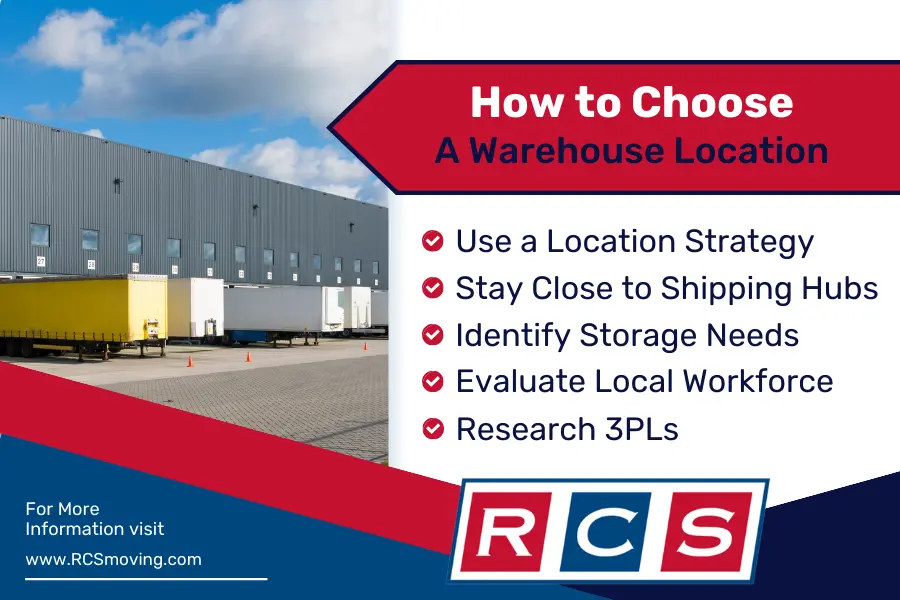
Targeted Location Strategy: Select a site that is in close proximity to your core customer base. This strategic decision can lead to quicker deliveries and lower shipping costs, enhancing customer satisfaction overall.
Nearness to Shipping Hubs: Locate your warehouse close to major carrier hubs to simplify and expedite shipping processes. This balance optimizes both customer convenience and logistical efficiency.
Tailored Storage Solutions: Your warehouse should cater to the specific requirements of your products, whether that involves special handling, refrigeration, or extra care for fragile items. Also, anticipate your future growth and opt for a facility that can accommodate evolving needs.
Workforce Dynamics: Evaluate the labor market around the potential warehouse site. Factors like workforce availability, unemployment rates in the area, and the technological capabilities of the warehouse directly affect operational productivity and the effectiveness of automated systems.
Warehouse or 3PL Decision: Consider if a traditional warehouse setup or a partnership with a third-party logistics (3PL) provider better suits your business model. 3PLs offer scalability and flexibility, which might be more advantageous depending on your operational needs.
Effective Warehouse Management System (WMS): Implement a robust WMS that can scale with your business. An effective WMS enhances labor productivity and boosts customer satisfaction levels.
Incorporating these key elements into your decision-making process will help you select the most suitable warehouse location in Virginia, ensuring a balance between operational efficiency, cost-effectiveness, and customer satisfaction, thus supporting your business's expansion and success.
Warehouse Inventory Management and Assessment
To ensure a seamless warehouse relocation, it's essential to methodically handle each aspect, optimizing inventory for efficiency in the new location. Efficient inventory management is vital for a smooth move, involving both relocating items and maintaining easy access post-relocation. With the right strategies, this process can become manageable and empowering.Let's break it down.
Inventory Auditing: Conduct comprehensive checks to maintain an accurate inventory count. This step is crucial for identifying what you have, what's missing, or what's excess before the move.
Categorization: Sort items for efficient unpacking and organization at the new location. Grouping similar items together aids in faster setup and minimizes operational downtime.
Labeling and Tracking: Implement a system for easy tracking and identification. This can involve barcoding or RFID tags, ensuring every item is traceable throughout the move.
Storage Solutions: Plan storage logistics for both during and after the move. Determine the appropriate storage solutions and layouts that optimize space and accessibility in the new location.
Disposal of Unnecessary Items: Eliminate items that are no longer needed to streamline the move. This not only reduces moving costs but also declutters your new space for better efficiency.
Data Backup: Securely store inventory data to prevent loss during transition. Backing up data in cloud-based or offsite storage ensures continuity and quick recovery in case of any data mishaps.
How to Transfer Equipment and Machinery to New Warehouse Location
Moving equipment and machinery requires meticulous planning and execution to ensure everything arrives safely and is ready for operation. This task can be complex, but with a structured approach, you can transition smoothly and efficiently. Let's explore how to do this effectively.
Professional Assessment: Get expert input on the best ways to transport your machinery. Specialists can advise on the safest and most efficient methods, tailored to your specific equipment.
Appropriate Packaging: Use protective materials to safeguard equipment during the move. This includes using padding, wraps, and crates designed to protect against shocks and vibrations.
Transport Logistics: Strategize the movement of large or delicate machinery. This may involve hiring specialized transport vehicles and planning the route meticulously to avoid complications.
Customized Handling Instructions: Develop and communicate specific handling instructions for each piece of machinery. Custom instructions are crucial, especially for specialized or delicate equipment, as it guarantees that every item is treated with the necessary care and expertise throughout the relocation process.
Installation Plans: Prepare for quick and efficient setup at the new site. Having a clear plan for installation means less downtime and faster return to operational capacity.
Testing Post-Move: Check all machinery for functionality after installation. This step is essential to ensure everything is working correctly and to address any issues caused by the move.
Warehouse Safety and Regulatory Considerations
Ensuring safety during a warehouse move is paramount to keeping your team and equipment safe. This requires a focus on compliance, training, and preparedness. Let's delve into the key considerations to maintain a high safety standard during the move.
Compliance Checks: Verify that the new location meets all safety standards. This involves ensuring that the new warehouse complies with all relevant health and safety regulations, providing a safe environment for your team and goods.
Employee Training: Educate your team on safe moving practices. Comprehensive training on safe handling, equipment use, and emergency procedures is essential for reducing the risk of accidents.
Equipment Safety: Ensure all moving equipment is up to safety standards. Regularly check and maintain equipment such as forklifts, pallet jacks, and conveyor systems to prevent malfunctions.
Emergency Plans: Be prepared for any incidents during the move. Develop and communicate clear emergency response plans for different scenarios to ensure swift and effective action when needed.
Regular Inspections: Monitor the moving process for potential hazards. Conducting ongoing inspections throughout the moving process helps identify and mitigate risks early.
Reporting System: Set up a protocol for reporting safety issues. A well-defined system for reporting and addressing safety concerns is vital for maintaining an ongoing focus on safety.
Additional Tips for a Successful Warehouse Relocation
When it comes to relocating a warehouse, the process is complex and has a significant impact on your business operations. To help you navigate this challenging endeavor successfully, consider the following additional tips:
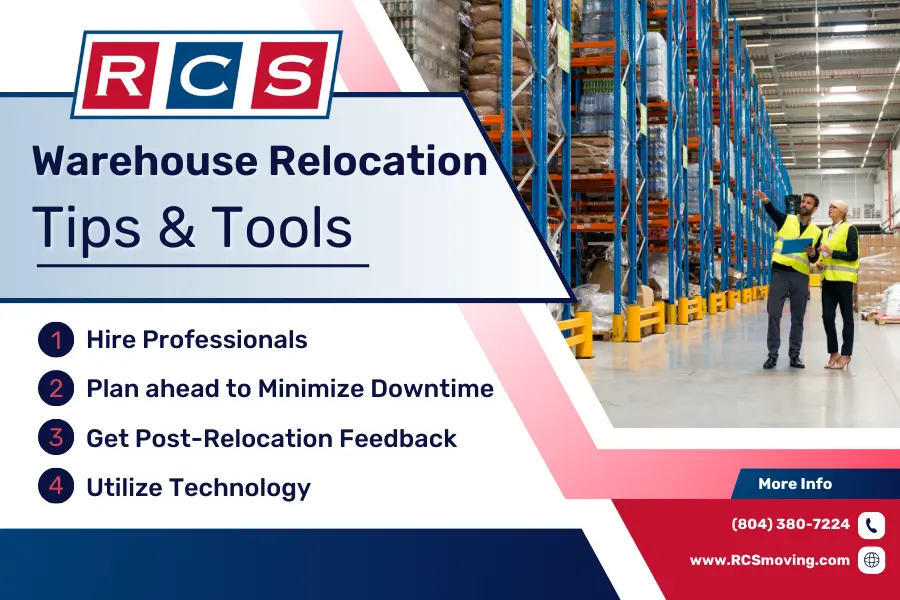
Hire Professional Movers: Engage experts for their experience and efficiency. This ensures a smoother move, access to specialized equipment, risk management, insurance coverage, and reduces stress on your team.
Minimize Downtime: Prepare in advance, move in phases to keep some operations active, set up backup operations, use technology for smooth transitions, and have support ready for immediate post-move issues.
Stakeholder Communication: Regularly update stakeholders, maintain transparency, encourage feedback, hold meetings for alignment, establish clear communication channels, and provide a comprehensive post-move report.
Post-Relocation Evaluation: Evaluate the relocation's effectiveness, gather feedback for improvements, implement necessary adjustments, document the process, focus on continuous improvement, and celebrate your team's success.
Choosing RCS Moving for Your Warehouse Relocation Service Needs
A warehouse relocation requires expertise, precision, and comprehensive planning. RCS Moving and Storage, serving Virginia and North Carolina, stands as an exemplary choice for this crucial task, offering professionalism and tailored solutions for a seamless relocation.
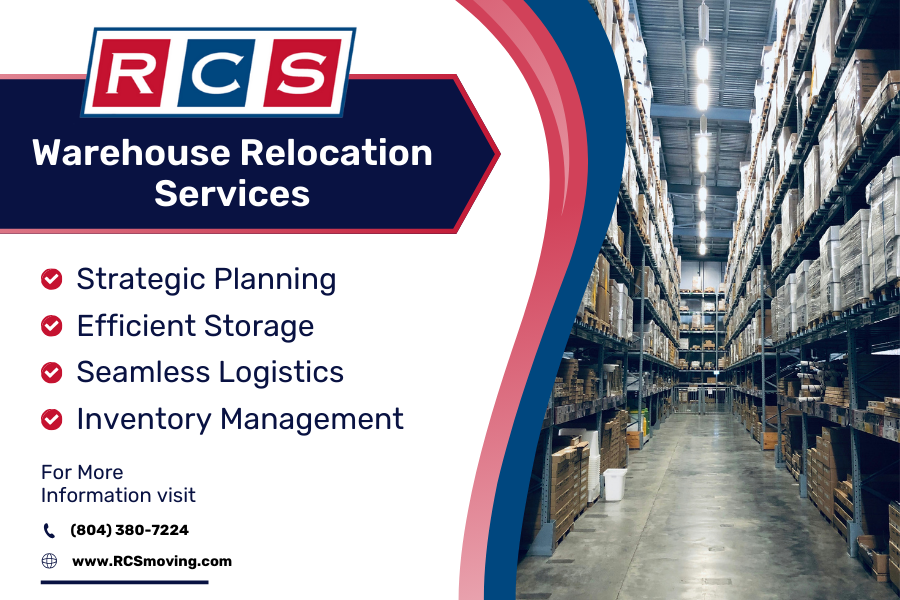
Expertise in Commercial Moving
With 30 years of experience, RCS provides unparalleled proficiency in commercial relocations. Our deep understanding of the unique challenges and requirements of commercial moves ensures that your relocation is handled with the utmost care and efficiency.
Diverse Service Portfolio
Their services extend to logistics, installation, and storage solutions, meeting a wide range of business needs. This versatility makes RCS a one-stop-shop for all your moving needs, simplifying the relocation process and providing convenience.
Professional Installation Services
Specialized in FF&E installation, ensuring smooth setup in new locations, ideal for retail and hospitality sectors. This service is crucial for businesses that require a quick and efficient setup to minimize downtime and resume operations swiftly.
Comprehensive Storage Options
Offering warehouse storage for various items, including office furniture, equipment, and supplies. This feature is particularly helpful for businesses that need temporary storage solutions during the relocation process or extra space for inventory.
Customized Local and Long-Distance Moving
Tailored moving plans for both local and interstate relocations, handled with personalized care. Whether you're moving within the state or across state lines, RCS provides a customized approach to meet your specific needs.
Eco-Friendly Cleaning Services
Providing top-tier commercial cleaning with a focus on eco-friendly solutions, perfect for enhancing workspaces post-relocation. This service is especially beneficial for businesses looking to maintain a clean and healthy environment for their employees and customers.
FAQ Section
Q1. How do I make the relocation process easier for my team?
A1. Involve your team in the planning process, communicate openly, and ensure their needs and concerns are addressed for a smoother transition.
Q2. What should I prioritize when choosing a new warehouse location in Virginia?
A2. Prioritize factors like accessibility to transportation, proximity to your workforce, and alignment with your business's growth strategy.
Q3. Can a warehouse relocation actually benefit my business in the long run?
A3. Absolutely. Relocating offers a chance to streamline operations, access new markets, and foster a renewed sense of purpose within your team.
Q4. How can I ensure minimal disruption to my customers during the relocation?
A4. Plan the move in phases, maintain a buffer stock to fulfill orders, communicate anticipated delays, and consider temporary outsourcing or partnerships to manage customer needs.
Q5. What are the best practices for managing inventory during a warehouse relocation?
A5. Conduct a thorough inventory audit before the move, use this opportunity to declutter and liquidate excess stock, clearly label and categorize items for efficient unpacking, and employ inventory management software for tracking and seamless transition.